Today, steam boilers are of significant importance due to their vital role in producing steam for thermal power plants, refineries, the food industry, and heating systems. These devices convert thermal energy into steam, which serves as an efficient energy carrier used to drive turbines and generate electricity. Furthermore, steam can facilitate heat transfer in heating systems or support chemical processes in diverse industries. Through advanced technologies and renewable energy sources, steam boilers contribute to lowering pollutant emissions and increasing energy efficiency. These attributes make them crucial for sustainable development.
What is a Steam Boiler?
A steam boiler is a device that produces steam by converting water into steam through thermal energy. The energy derived from fossil fuels (such as natural gas and oil) is transferred to water, causing it to heat up and eventually turn into high-pressure, high-temperature steam. The produced steam is used as one of the key energy sources in various industries. It can be used as a heat source for heating purposes or for electricity generation.
Different Types of Steam Boilers
Steam boilers are structurally divided into two main categories: water-tube and fire-tube. Both designs have their specific advantages and disadvantages, making them suitable for various purposes.
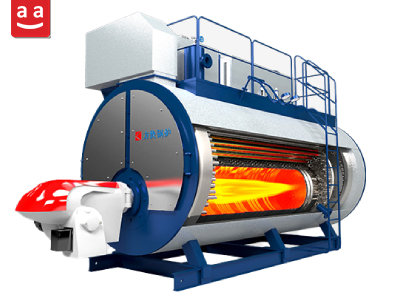
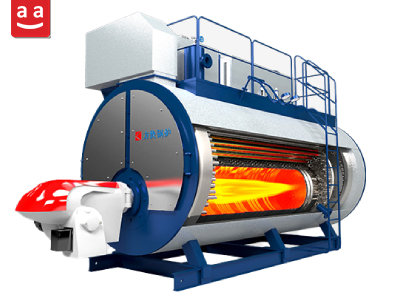
Fire-Tube Steam Boiler
In this type of steam boiler, hot gases generated from combustion flow through tubes, while water surrounds these tubes. The heat is transferred to the water through the tube walls, turning it into steam. These types of boilers are ideal for generating steam at low to medium pressures.
Advantages: Simple construction, lower cost, and suitable for medium and low capacities.
Disadvantages: Lower thermal efficiency and reduced steam pressure capacity compared to water-tube boilers.
Water-Tube Steam Boiler
In this type of boiler, water flows within the tubes, and the heat from hot combustion gases, which are located outside the tubes, turns the water into steam. These boilers are particularly designed for producing steam at high pressures and temperatures. They are commonly used in large-scale industries and power plants.
Advantages: Higher thermal efficiency, higher steam pressure generation capacity, and suitable for large capacities.
Disadvantages: More complex design and higher costs.
To gain a deeper understanding of this type of boiler, it is suggested to check out the article “A Complete Guide to Water-Tube Boilers: A Detailed Comparison with Fire-Tube Boilers “.


Steam Boiler Components
Both fire-tube and water-tube steam boilers are made up of various components, each of which plays an important role in the proper operation and efficiency of the boiler. This article will explore each of these components.


Burner
One of the main components in a steam boiler is the burner, which plays a pivotal role in the combustion process. The burner’s main function is to mix fuel (such as gas, oil, or heavy oil) with the air required for combustion in the proper ratio. This mixture leads to the formation of a stable and efficient flame that supplies the heat needed to warm the water and convert it into steam. The proper design of the burner has a remarkable impact on steam production and the boiler’s efficiency.


Combustion chamber
Another key component of the steam boiler is the combustion chamber, where the fuel combustion takes place. In this section, the heat generated from combustion is transferred to the water, resulting in steam production. The combustion chamber design must ensure that combustion is as complete as possible and prevent the formation of pollutants like NOx and carbon dioxide. The combustion chamber’s dimensions must be carefully designed to prevent direct contact between the flame and the chamber walls. Therefore, Choosing the right burner for the boiler is crucial for ensuring efficient combustion and optimal performance.
Water Tubes and Smoke Tubes
In water-tube steam boilers, water flows through tubes that absorb heat from combustion gases, producing high-pressure steam. In contrast, fire-tube boilers pass combustion gases through smoke tubes, transferring heat to the water surrounding them.
In fire-tube steam boilers, combustion gases flow through the smoke tubes, transferring heat to the water around them. Fire-tube boilers are typically used for generating steam at low to medium pressures.
Stack
The stack in a steam boiler plays a crucial role in directing combustion gases outside the system. The height of the stack is vital for the efficient operation of the steam boiler system and for ensuring proper draft for the expulsion of combustion products.
Economizer
An economizer is a type of heat exchanger used in steam boiler systems to recover heat from the combustion gases before they enter the stack. In the economizer, heat is exchanged between the hot gases and the boiler feedwater, raising the water temperature. This reduces the amount of energy required for converting water into steam, leading to lower fuel consumption, reduced operational costs, and enhanced boiler efficiency.


Superheater
Another type of heat exchanger is the superheater, which converts saturated steam into superheated steam. The use of a superheater in steam boilers provides notable benefits, such as improved thermal efficiency, lower fuel consumption, and enhanced steam quality. By increasing the steam temperature above the saturation point, the superheater enhances system performance and allows for the generation of higher-quality steam at greater pressures. This results in an increase in the boiler’s output and a reduction in operational costs.
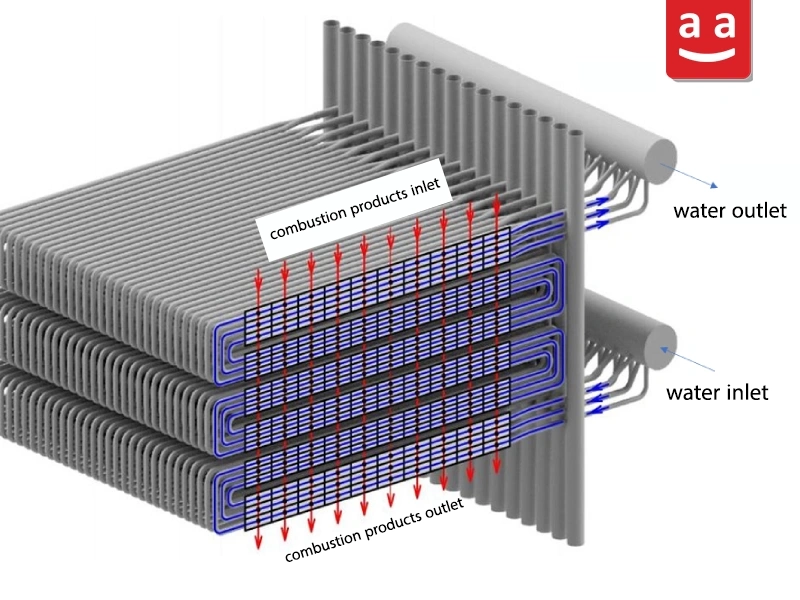
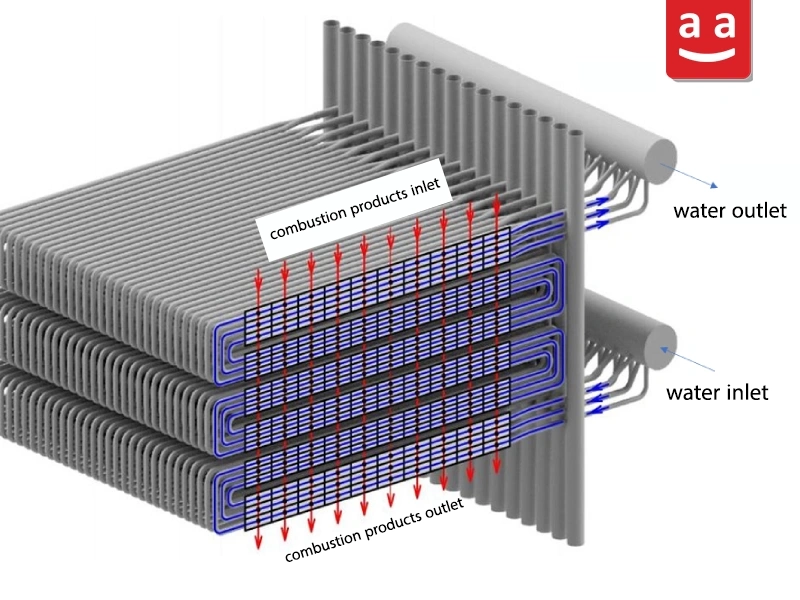
Relief Valve
The relief valve is a critical component of a steam boiler, designed to prevent excessive pressure buildup. If the pressure exceeds safe limits, the valve automatically opens to release steam, preventing potential hazards such as explosions or equipment damage. This safety feature ensures the boiler operates within safe pressure ranges, maintaining both efficiency and safety.


Blowdown Valve
It is another part of the steam boiler, installed at the bottom of the boiler to drain water and prevent the accumulation of scale. The accumulation of scale can lead to reduced boiler efficiency and pipe blockages. Regular use of the blowdown valve helps prevent the buildup of sediment and scale inside the boiler, ensuring efficient operation and extending the system’s lifespan.


Water Level Controller
Another essential piece of equipment in steam boilers is the water level controller, which is responsible for measuring and controlling the water level in the boiler. It continuously monitors the water level and transmits the data to the control system or operator to ensure adequate water is present in the boiler. The water level controller for steam boilers checks four water levels: low-low, low, high, and high-high.
- When the water level reaches the low-low state, both the pump and burner are automatically shut off, and an alarm is activated. At this point, the water level is so low that there is a risk of severe damage to the pipes.
- If the water level is at the low state, it means the water inside the boiler has decreased, and the water pump is turned on.
- In the high water level state, it indicates that more water than required has entered the boiler, and the pump is switched off.
- When the water level reaches the high-high state, the water surpasses the maximum allowed level, leading to the shutdown of the pump and burner, and the activation of the alarm system.
Packman Company uses capacitive and conductive modulating level controllers. Additionally, it employs smart burner and boiler controllers.


Thermometer and Manometer
Steam boilers use thermometer and manometer for measurement in the boiler system. These gauges instantly measure the temperature and pressure of the steam produced and provide the necessary information to the operator or control system. They help the operator ensure that temperature and pressure remain within safe and efficient ranges.


Boiler Control System
This system, known as the control panel, is specifically designed for monitoring, controlling, and managing the boiler and burner operations. It enables operators to check boiler key parameters in real time and make adjustments for optimizing performance and ensuring system safety. The main components of the control system include the display panel, sensors, PLCs, and safety systems. The AutoFlame controller is one of the top control systems used by Packman Company to manage both the boiler and burner simultaneously.


Apart from the main components, steam boiler rooms are equipped with numerous auxiliary devices. These include the feedwater pump, deaerator, condensate chamber, and blowdown chamber (bottom blowdown chamber). Additionally, reverse osmosis systems, filters, and water softeners are present in the boiler room. These components are vital for the efficient and safe operation of the steam boiler.
Feedwater Pump
In steam boilers, the feedwater pump is a type of multistage pump responsible for supplying water to the boiler. It transfers water from storage tanks into the boiler, supporting the continuous conversion of water into steam. The pump must provide sufficient pressure to overcome the high pressure inside the boiler. Typically, the feedwater pump is positioned after the deaerator.


Deaerator
It is a critical device in steam boiler systems. the main task of the deaerator is to remove dissolved gases, particularly oxygen and carbon dioxide, from the boiler feedwater. The presence of carbon dioxide in the water causes the formation of carbonic acid. The acidification of water leads to equipment corrosion and shortened service life. Therefore, removing these gases enhances equipment lifespan, boosts boiler efficiency, and cuts down on maintenance and repair costs. The deaerator operates by allowing the inlet water (usually a combination of condensate water and treated water) to enter from the top and then flow into the deaerator chamber.
A portion of the steam produced by the boiler enters the deaerator from the bottom, raising the temperature of the water inside. As the solubility of gases in water decreases with rising temperature, the steam increases the temperature of the water inside the deaerator, causing the dissolved oxygen and carbon dioxide gases to be separated and exit from the top of the deaerator. The water exiting the deaerator is then pumped into the boiler through the feedwater pump. Another advantage of using the deaerator is preheating the incoming water to the boiler to about 100°C.
Deaerators are typically positioned at a higher level than other equipment. This ensures that higher hydrostatic pressure is created at the boiler inlet and prevents cavitation from occurring in the feedwater pump.


Condensate Tank
This equipment collects and stores water resulting from the condensation of steam. When steam turns into water in heating processes or equipment like steam traps, the water returns to the condensate chamber. The condensed water still contains thermal energy, which can be reused. Therefore, the distilled water enters the deaerator, where dissolved gases are separated. Finally, this water is pumped back to the boiler through the feedwater pump to be converted back into steam.


Blowdown Tank
The water discharged from the blowdown valve is at a high temperature and pressure. To guide the blowdown water to the sewage system, it is necessary to discharge the flash steam from the pipes and reduce the temperature of the water entering the sewer. For this purpose, a blowdown tank is employed. When the high-pressure, high-temperature water enters the blowdown tank, its pressure is reduced. The flash steam is vented from the top section of the tank to the atmosphere, and the collected water from the bottom section flows into the sewer. A cooling fluid is utilized to lower the temperature of the water.
In some cases, to improve the system’s efficiency, the flash steam from the blowdown tank vent is directed to the consumer and used in a manner similar to the steam produced by the boiler. Moreover, the water inside the blowdown tank can be transferred to a heat exchanger to harness its energy, and after that, it can be discharged into the sewage system.


Reverse Osmosis
It is one of the water treatment techniques used to eliminate large particles like pollutants and salts from the boiler feedwater. Osmosis is a physical process where untreated water passes through a semi-permeable membrane. The semi-permeable membrane allows water molecules to pass while retaining salt, which is then removed from the system. Implementing reverse osmosis systems in steam boilers greatly enhances the quality of feedwater and aids in reducing the formation of scale in the boiler. Deposits formed by salt and other impurities can cause damage to equipment and reduce their lifespan.


Water Filter and Water Softener
Water filter and water softener are two vital pieces of equipment in the steam boiler system that help improve the quality of feedwater and prevent scale buildup. The water filter is used to remove larger pollutants from the feedwater. These filters are designed to pass water through multiple filter layers, capturing larger particles. This improves the feedwater quality and reduces the risks of scaling within the boiler. The water softener is employed to eliminate calcium and magnesium ions that contribute to water hardness.
These ions can lead to the formation of hard scale in the boiler, which in turn reduces the system’s efficiency and increases maintenance costs. Water softeners usually work through an ion exchange process, in which calcium and magnesium ions are exchanged for sodium ions, producing softer water for use in the boiler.


Steam Boiler Operation
The operation process involves converting water into steam and using it for energy or heating. To supply water, a feedwater pump is used, which pumps water into the boiler under pressure. Prior to entering the boiler, the water undergoes treatment in a reverse osmosis system and water softener, where harmful ions like calcium and magnesium are eliminated to avoid scale formation. The deaerator then removes dissolved gases such as oxygen and carbon dioxide to prevent damage to the equipment.
Within the boiler, fuel (like natural gas or oil) is mixed with air in the burner in the correct proportions. The combustion occurs, generating a flame, and the thermal energy from the exhaust gases is transferred to the water, turning it into steam. To enhance efficiency, an economizer is used to preheat the feedwater, while a superheater is used to produce superheated steam, utilizing the heat from exhaust gases before they exit the stack.
The condensate chamber is responsible for converting steam condensed in the steam traps back into water, which is then returned to the system. Ultimately, the generated steam is directed to consumer systems, such as steam turbines or heat exchangers, where thermal energy is converted into mechanical energy or heat.
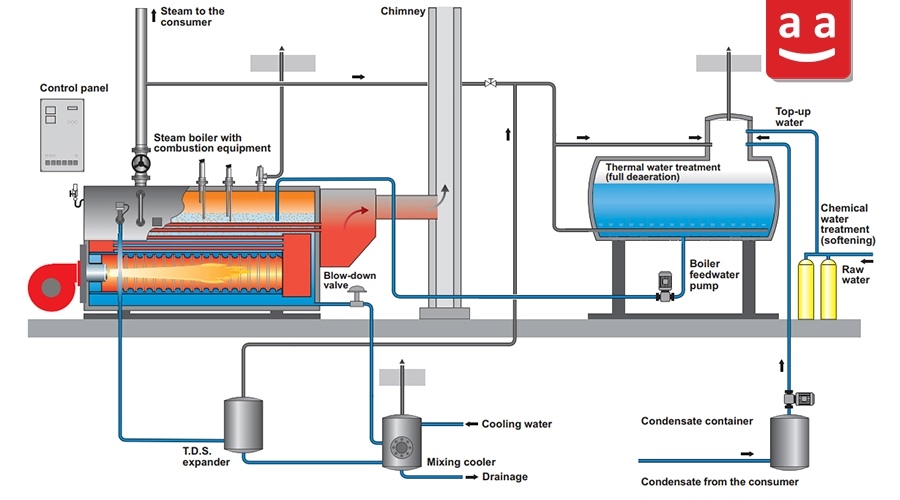
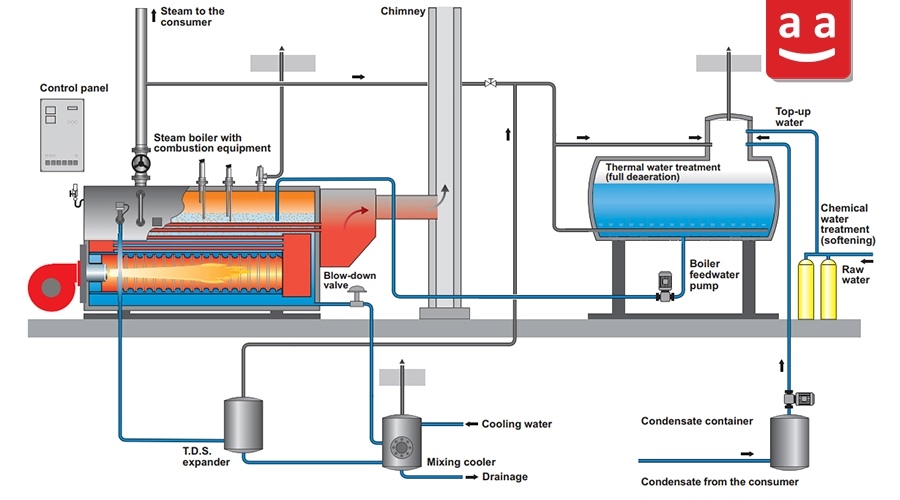
Applications of steam boilers
Steam boilers are used in industries to produce steam for different processes. This steam is crucial for electricity generation in power plants, heating in industrial exchangers, sterilization in the medical industry, and cooking in the food industry. In refineries, steam is also utilized for processes like distilling crude oil into various products, including gasoline, diesel, and other by-products.


Steam Boiler: The Key to Industrial Advancement
As one of the fundamental components in industrial processes, steam boilers play a key role in the progress and development of industries. With the ability to produce high-quality steam and provide the energy needed for heating systems, steam boilers help improve efficiency and reduce operational costs in industries. In this way, the steam boiler continues to serve as a key factor in industrial progress and is crucial for achieving sustainable development goals.
Packman industrial group produces a wide range of boilers, including water and steam boilers, with the goal of providing modern and efficient solutions for the thermal needs of industries. These boilers are designed to easily integrate with existing systems while ensuring the highest standards of safety and performance. Due to the group’s expertise in the boiler industry, Packman products are regarded as a reliable and cost-effective choice for various industrial sectors.