In gas transmission and distribution systems, using equipment capable of accurately and safely controlling gas pressure and flow is of critical importance. Gas regulators, or pressure regulators, are one of the key elements in these systems, designed to maintain safety, optimize equipment performance, and ensure pressure stability within a specified range. These devices are designed to transform high input pressure into a stable and appropriate pressure for various devices and processes. A wide range of balancers each with distinct features and applications, are employed in diverse industries, where the correct selection of type and brand plays a vital role in improving operational efficiency and equipment lifespan.
What is a regulator?
A regulator (balancer) is a mechanical or electronic device designed to control and regulate the pressure or flow of fluids such as gases and liquids. Its primary function is to convert high or fluctuating input pressure into a consistent, controlled output pressure, ensuring it meets various operational requirements effectively.
The key features of a regulator
A regulator is a device used to regulate and control pressure in various gas and liquid systems. It is designed to ensure system safety and optimal performance by reducing the input pressure to an appropriate level and maintaining it consistently at a specified value.
1- Regulating and stabilizing the pressure: The primary function of a regulator is to reduce high and unstable input pressure to a stable and suitable output pressure, ensuring the safety and optimal performance of the system.
2- Controlling the flow: These devices can adjust the fluid (gas or liquid) flow rate according to the system’s needs. This feature is particularly important in industries and critical applications.
3- Stability in output pressure: A reliable regulator must have the ability to sustain a constant output pressure despite fluctuations in input pressure. This stability contributes to optimal operation of equipment which are connected to the regulator.
4- Safety: These devices mitigate the risks of overpressure by regulating and controlling pressure and help reduce the risk of explosions or equipment failure.
5- Prompt response to pressure changes: A regulator must be capable of rapidly reacting to changes in input or output pressure in order to maintain the pressure within an appropriate range.
6- Flexibility: They can be designed for various types of gases and liquids, and are used in a wide range of industries, including residential, industrial, medical, and laboratory applications.
7- Manual and automatic adjustment capability: While some balancers allow for manual adjustment, advanced types can be automatically adjusted using electronic control systems.
8- Compatibility with various environments: Balancers must be made of durable materials to withstand corrosion, heat, and extreme pressures in different environments.
9- Durability and lifespan: Regulators, due to their use in critical systems, must have high durability and reliability to operate long-term without the need for frequent repairs.
10- Compatibility with various pressure ranges: These devices can be designed and employed in low, medium, and high-pressure ranges based on the specific application and system needs.
11- Simplifying the operation of gas and liquid systems: Regulators contribute to the ease of operation in gas or liquid systems by controlling pressure and flow. So, they reduce the complexities related to pressure control in these systems.
The Significance of using a Regulator
Using regulators in various gas and liquid systems is highly important due to the key role in regulating and controlling pressure. They not only enhance safety but also ensure optimal system performance. The primary reasons and significance of using a balancer are highlighted below.
1- Safety maintenance: Regulators keep gas or liquid pressure within a safe range, preventing incidents caused by high pressure, such as explosions or leaks. This is particularly important in industries dealing with flammable gases like natural gas or LPG, where accurate pressure regulation is vital. Moreover, excessive pressure can damage pipes, fittings, and other equipment. By controlling both input and output pressures, the regulator helps prevent system failure.
2- Enhancing system efficiency and performance: Numerous devices and systems depend on a specific and stable pressure to operate correctly. Regulators keep this pressure at an optimal level to ensure high-efficiency operation. Furthermore, accurate pressure regulation also helps reduce energy consumption and optimize processes.
3- Precise Pressure control: In some industrial or laboratory applications, precise pressure control is required. Advanced regulators can precisely adjust pressure within specified ranges and prevent undesired fluctuations in the system. Furthermore, regulators can rapidly respond to changes in input pressure and regulate output pressure according to the system’s requirements.
4- Extending Equipment Lifespan: Regulating pressure helps prevent damage caused by sudden and uncontrolled pressure fluctuations. This can contribute to increasing lifespan of equipment and minimizing repair and maintenance costs. This can extend the useful life of equipment and reduce maintenance and repair costs. Additionally, pressure-sensitive equipment needs to operate under optimal conditions, and the regulator prevents damage due to fluctuations or pressure spikes.
5- Improving safety in residential applications: In residential settings, gas regulators are used to regulate the gas pressure supplied to appliances such as stoves, heaters, and water heaters. These appliances require a consistent gas pressure for safe operation, which is ensured by regulator.
6- Application in critical industries: In petrochemical, oil, and gas sectors. precise control of gas and liquid pressure is critical. Regulators are used in gas trains, refineries, and petrochemical facilities as essential tools to ensure safety and manage complex processes. Additionally, in medical devices like anesthesia machines and oxygen supply systems, controlling gas pressure is vital, and precise regulators play a significant role in ensuring patient health and safety.
7- Controlling Flow and optimizing gas consumption: In heating and energy supply systems, precise regulation of gas flow helps optimize fuel consumption, reduces unnecessary gas usage, and leads to lower energy expenses.
8- Adaptation to Changing Environmental Conditions: In some regions, gas or liquid pressure may fluctuate due to changes in temperature or environmental conditions. Regulators can respond to these fluctuations and keep the pressure at an optimal level. Furthermore, in high-altitude areas where atmospheric pressure is lower, regulators help ensure that the pressure of gases or liquids in systems is properly adjusted.
What is gas a regulator?
A gas regulator, also known as a balancer, stabilizer, or governor, is a device designed to adjust and control the pressure of gas from high-pressure sources (such as gas cylinders, tanks, or gas lines) to a stable and appropriate output pressure for safe use in various equipment. These devices are of critical importance because, without them, the gas pressure in different systems can become unstable or too high, leading to serious hazards such as explosions or equipment failure.
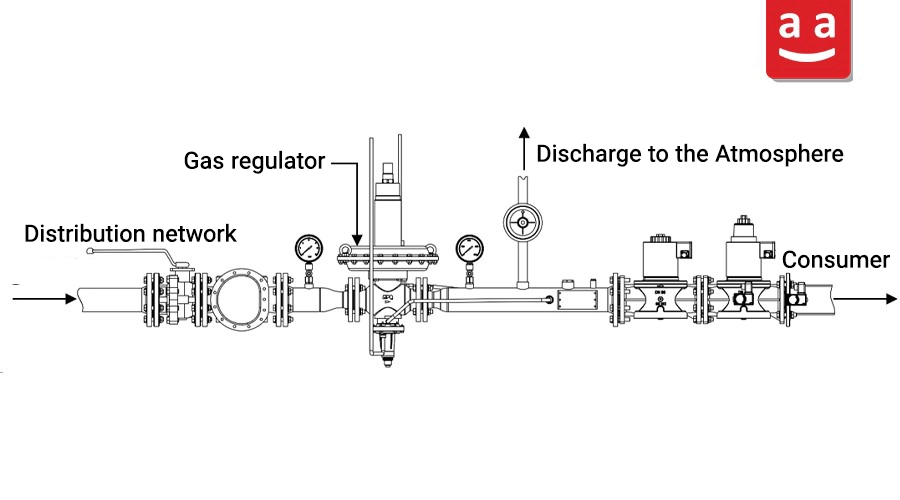
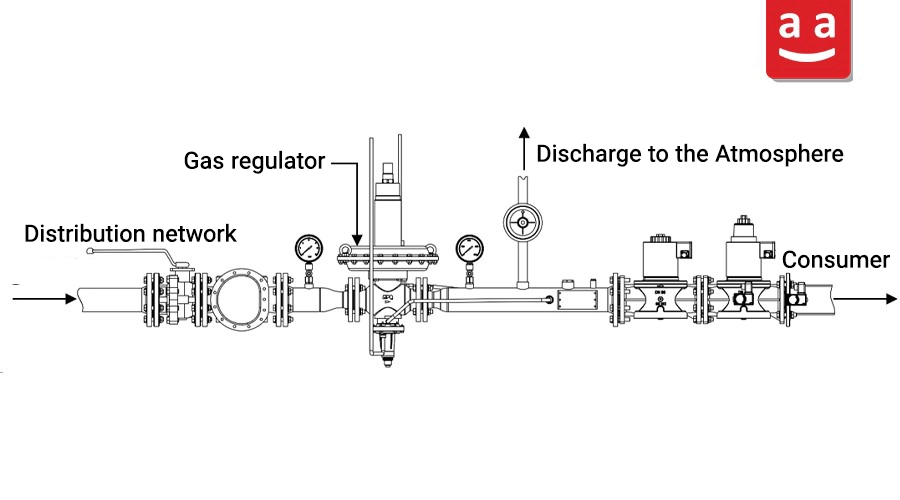
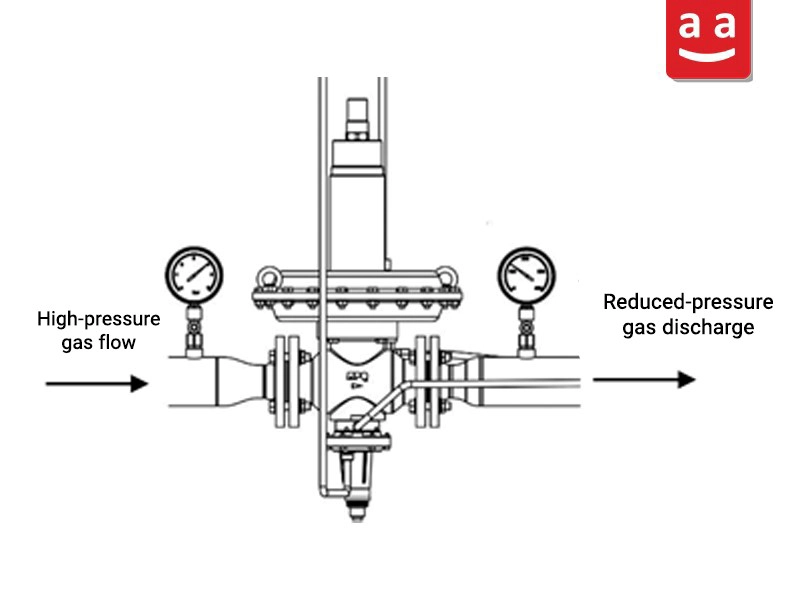
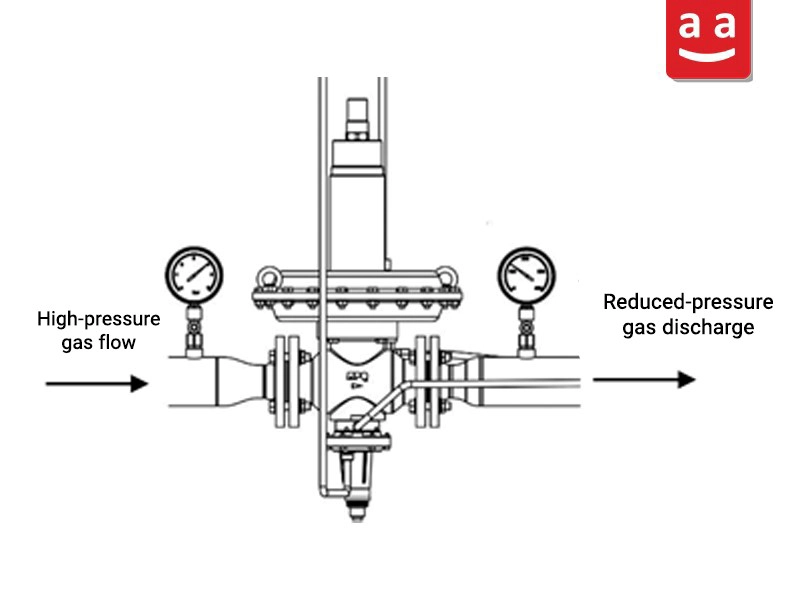
Different Types of Gas Regulators
According to the input gas pressure, these devices are categorized into different types, which are explained below.
Low pressure: This type of regulator is commonly used for gases like natural gas or propane, which are supplied at high pressure, and it reduces their pressure to a safe level for consumption by devices. The pressure adjustment in these types of regulators is done using a diaphragm and spring mechanism. The output pressure of such regulators typically ranges from 0 to 0.5 bar.
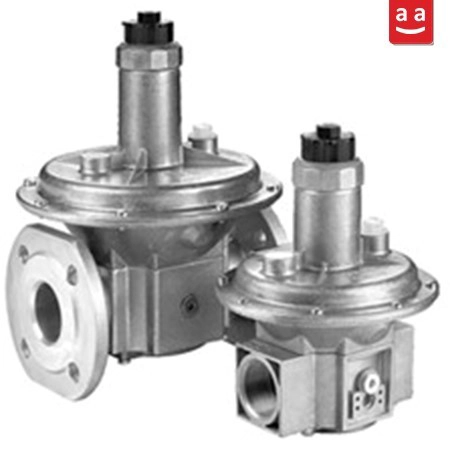
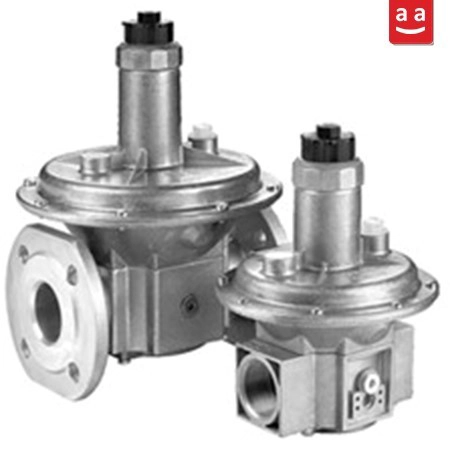
Medium pressure: This type of balancer is used to adjust and reduce the inlet gas pressure within a medium pressure range. It is designed for systems that require a pressure higher than low pressure but lower than high pressure, and is commonly used in industrial, commercial, and some specific residential applications. The pressure adjustment in these types of regulators is done by a diaphragm and spring mechanism. The output pressure of these regulators typically ranges from 0.1 to 4 bar.
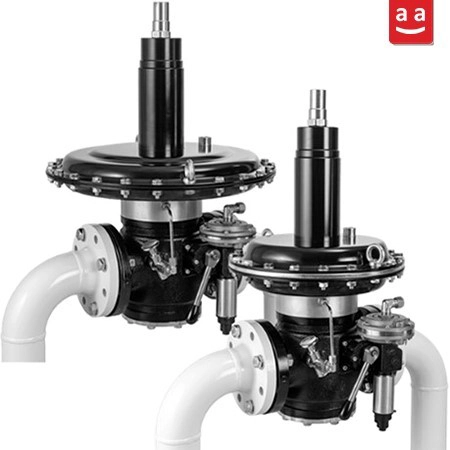
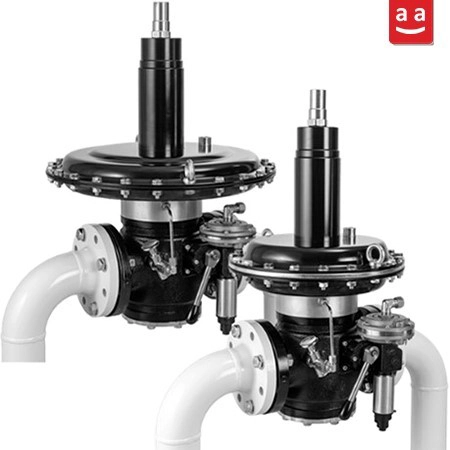
High pressure: This type is used to adjust and reduce the inlet gas pressure in very high ranges. It is designed to reduce high-pressure gases to a controllable output pressure suitable for use in specific industrial, medical, and laboratory systems. Pressure regulation in these types of balancers is done by a diaphragm and spring mechanism, which operates through a control valve connected to the diaphragm and spring. The output pressure of these regulators typically ranges from 0.1 to 34 bar.
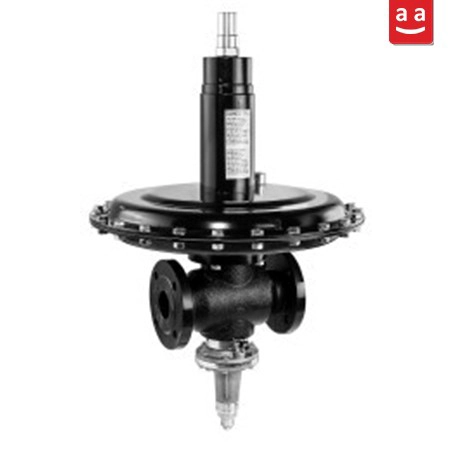
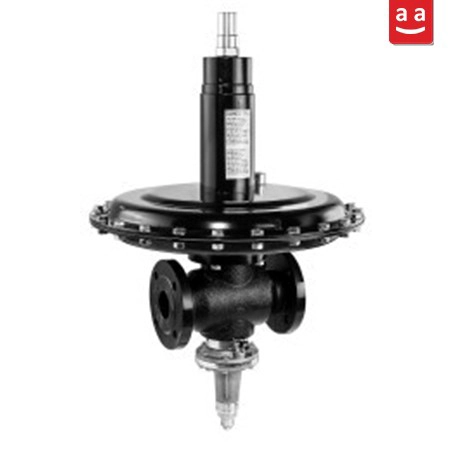
Pulse-line: A pulse-line gas regulator is designed to control pressure using a specific method. This type is commonly used in industrial systems and applications that require precise pressure control, particularly where the gas flow fluctuates in a pulsed manner. In this type, pulse signals are sent to the regulator to adjust the pressure. Due to the use of pulse lines, these devices can regulate pressure and quickly respond to rapid changes in input pressure and load demand. The output pressure of these regulators typically ranges from 0.1 to 34 bar.
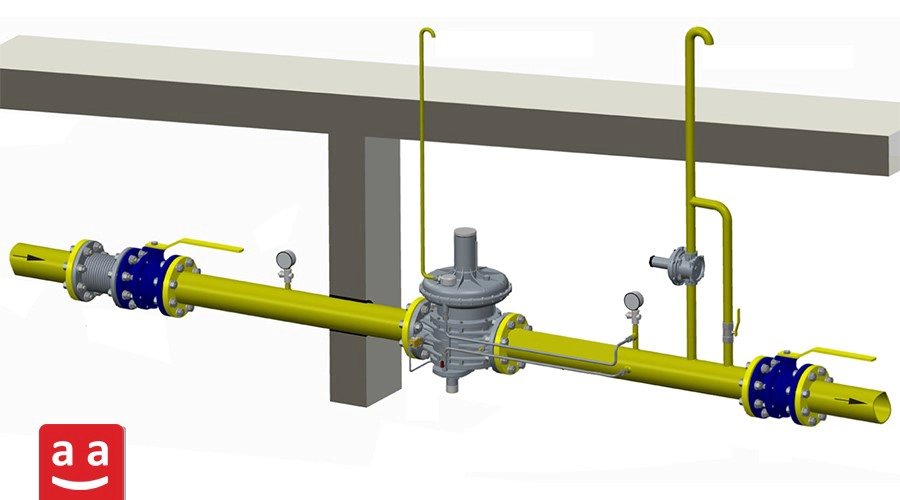
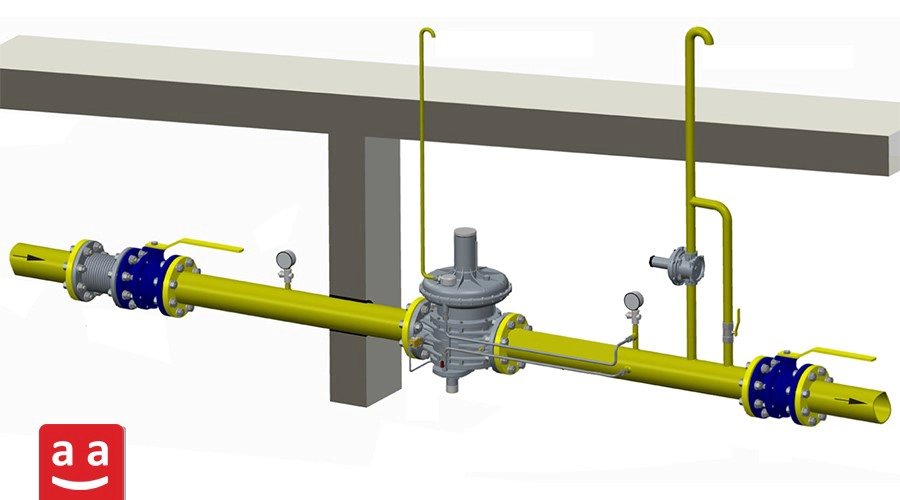
Pilot-operated: It is designed for precise pressure control using a pilot system. This pilot system includes a separate control valve that sends the necessary signals to the main regulator to adjust the pressure. These types of regulators are typically designed for applications requiring high accuracy and complex conditions. The pressure adjustment in these regulators works as follows: The pilot valve independently controls the pressure on a smaller scale and sends signals to the main regulator. The main regulator then responds to the signals received from the pilot and adjusts the output pressure according to the pilot’s settings. The output pressure range of these regulators typically falls between 0.1 and 34 bar.
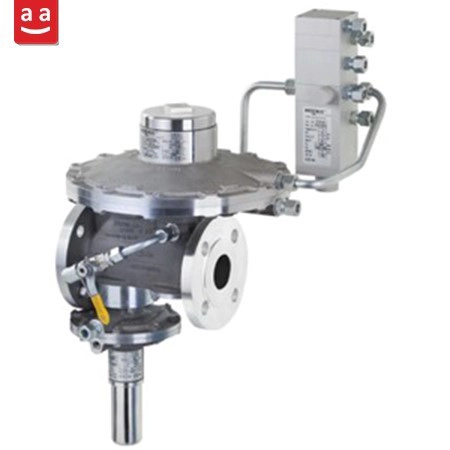
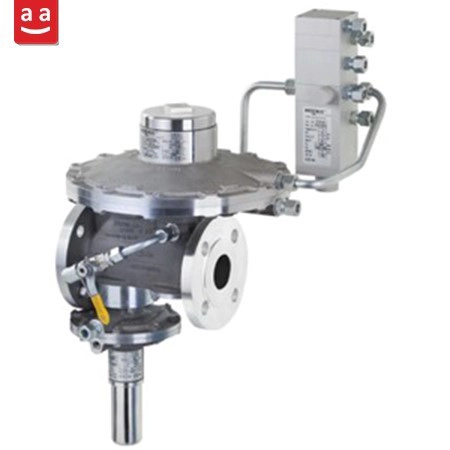
Zero governor: It is a type of balancer that adjusts the output gas pressure to a level very close to zero, or slightly above atmospheric pressure. This type is designed for systems that require very low input pressure, such as specific burners and boilers that need a stable and low gas pressure for proper operation. Pressure regulation to near zero in these regulators is achieved by the internal system (usually consisting of a diaphragm and spring), which reduces the inlet gas pressure to a level close to zero.
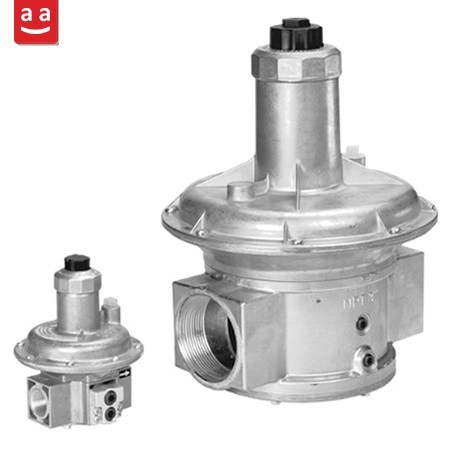
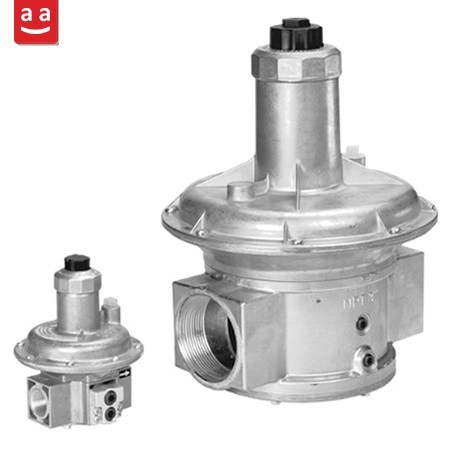
Single stage gas: This type is designed to reduce gas pressure from a higher level to a lower, stable level in a single stage. It is the simplest and one of the most commonly used types of balancers. The pressure regulation is accomplished by a diaphragm and spring mechanism, where the diaphragm transmits the gas pressure to the spring, reacting to fluctuations in the input pressure. The output pressure range for these devices typically falls between 0.1 to 5 bar.
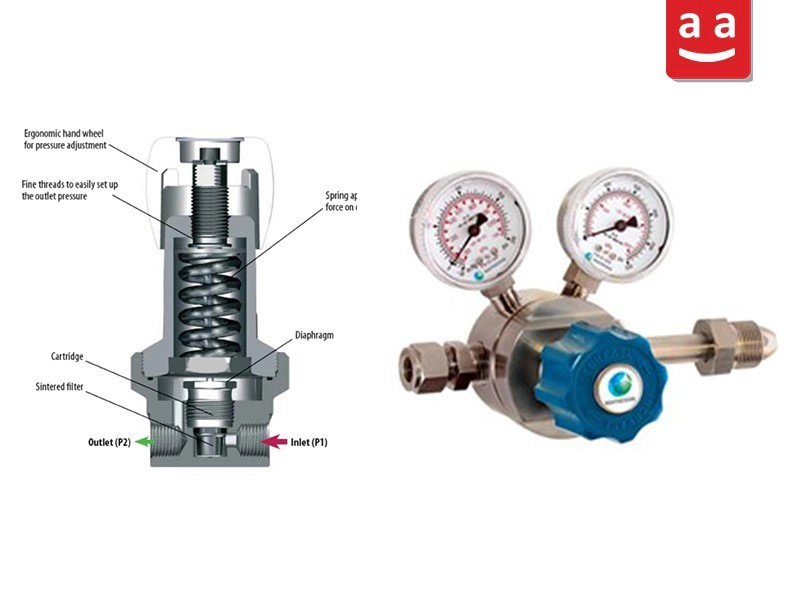
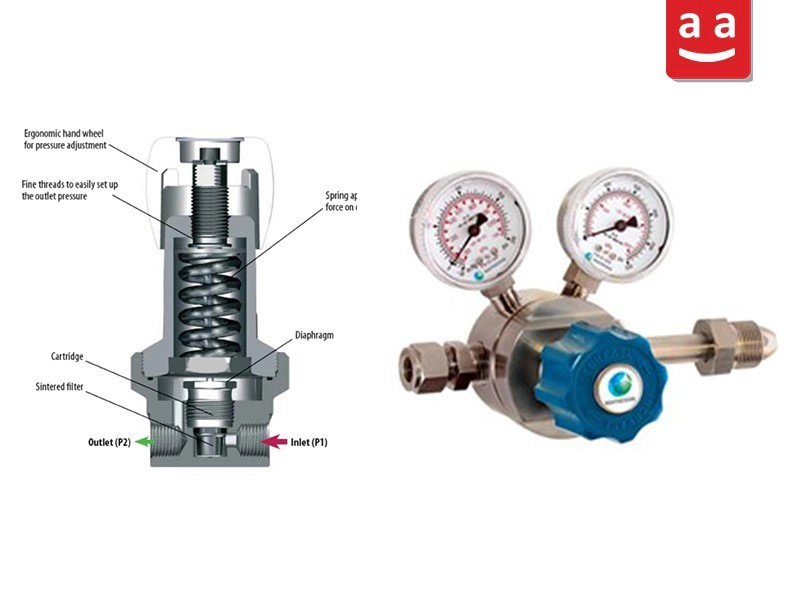
Two Stage: This type is specifically designed to reduce gas pressure in two stages. It is ideal for applications which demand more precise pressure control and better stability against input pressure fluctuations. The operation occurs as follows: during the first stage, the input gas pressure is reduced to an intermediate level, which is typically higher than the final output pressure. The intermediate pressure serves as a constant pressure for the second stage. In the second stage, the intermediate pressure is reduced to the final output pressure, which is then delivered to the consumer equipment. Pressure regulation in this type of regulator is achieved through the use of a valve and diaphragm. The output pressure range is generally between 0.1 and 5 bar.
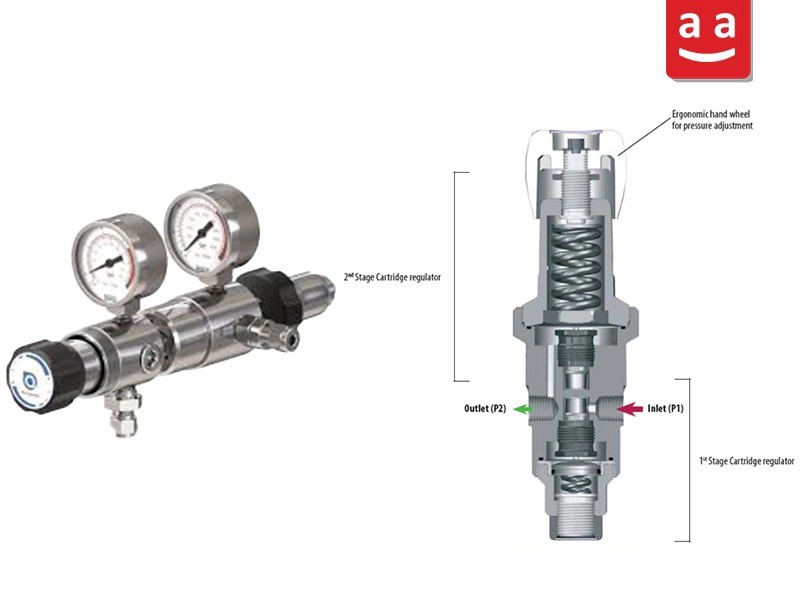
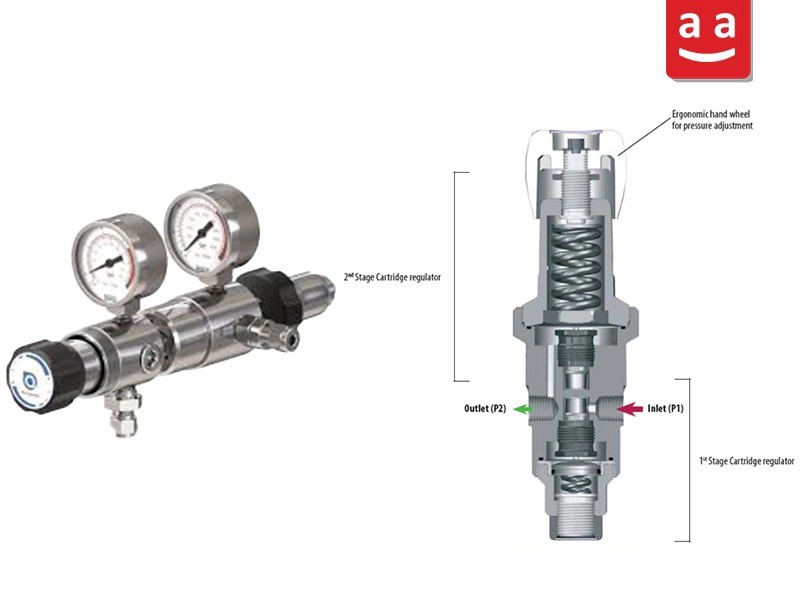
Self-operated: This type automatically maintains and adjusts the output pressure without the need for continuous manual adjustment. This balancer automatically responds to changes in input pressure and operating conditions, keeping the output pressure at the desired level. The self-operated balancer continuously adjusts the output pressure to match changes in input pressure and operational conditions. The pressure adjustment in these devices is automatic, ensuring the output pressure remains optimized and stable. This adjustment can be either electronic or mechanical and typically involves continuous adjustments. The output pressure of these regulators typically ranges from 0.1 to 10 bar.
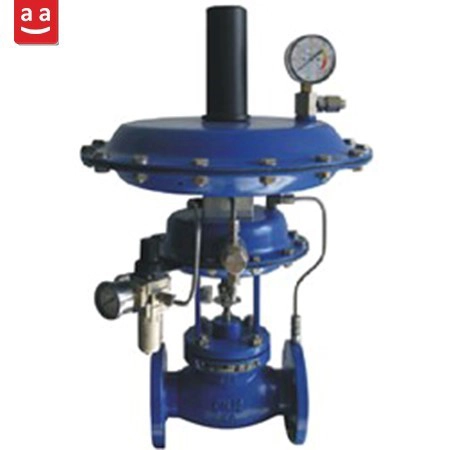
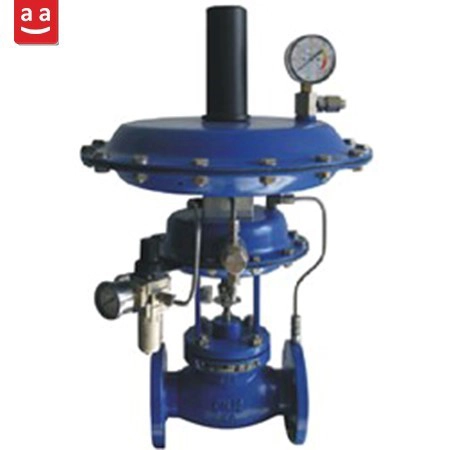
Electronic: This type uses electronic technologies instead of mechanical or manual methods to control and adjust gas pressure. These balancers are widely used, particularly in critical and complex systems, due to their high accuracy and automatic capabilities. Electronic gas regulators are equipped with pressure and temperature sensors that send data to the control circuit. The electronic circuits are responsible for adjusting and maintaining the pressure. These devices are highly precise, making them ideal for applications where consistent pressure is critical. The output pressure of these balancers typically ranges from 0.1 bar to 34 bar, though the specific range can vary depending on the type and specific application of the balancer.
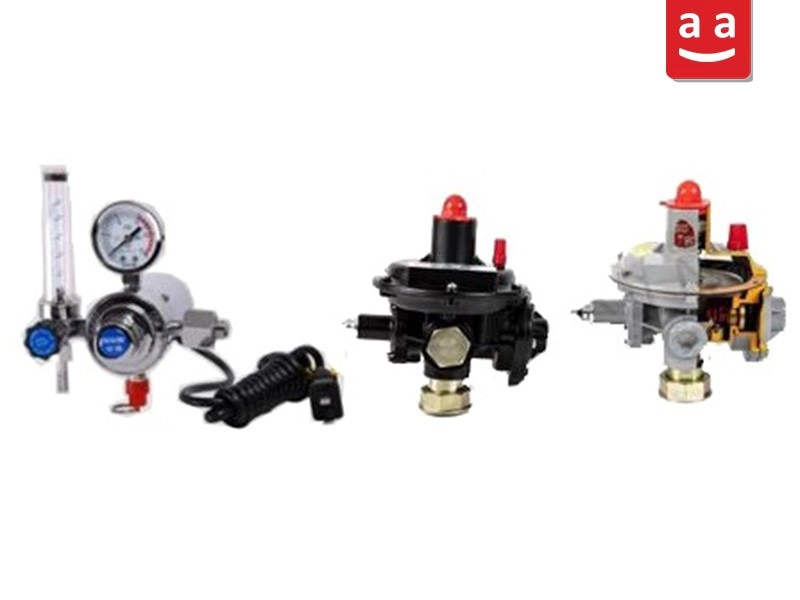
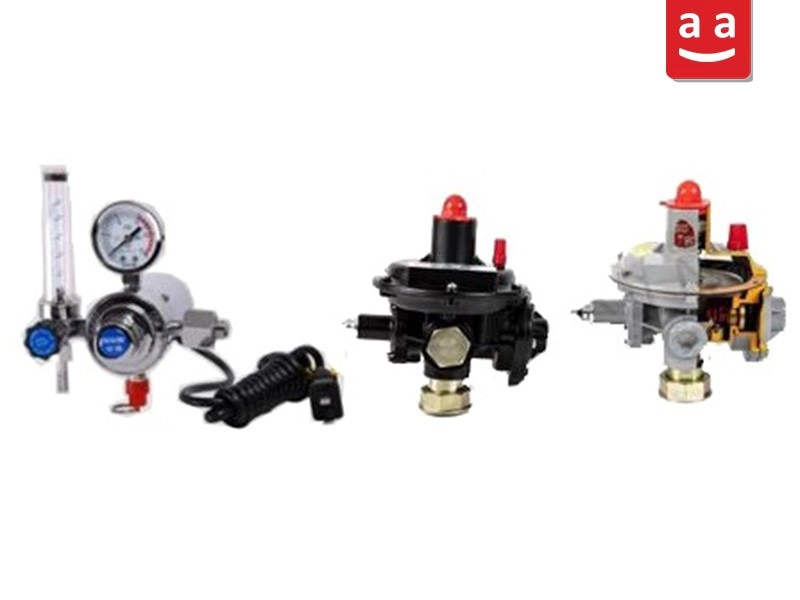
Piston: It is a type of gas regulator that uses a piston as the main element for adjusting and controlling pressure. These regulators are widely used in various industrial and commercial applications due to their high precision and specific capabilities in pressure regulation. The pressure adjustment in these regulators operates by the piston responding to changes in input pressure. The piston mechanically adjusts the output pressure, with the output pressure being regulated through the movement of the piston. The output pressure of these regulators typically ranges from 0.5 bar to 15 bar.


Top Gas Regulator Brands in the Market
Determining the best gas regulator brand can be challenging due to the similar quality levels, varying needs, and expert opinions influenced by personal preferences. However, some well-known foreign brands include Dungs, Kromschroder, RMG, Madas, and Elster Jeavon. In the Iranian market, Gas Souzan and Setak are among the recognized local brands.
To choose the right gas regulator, you should define your system’s specific needs and seek advice from qualified professionals to select a brand that aligns optimally with your requirements.
Gas Regulator Maintenance and Repair
Ensuring the efficiency and longevity of gas regulators requires proper adherence to routine maintenance and repair guidelines. Below, we highlight key tips in this regard:
- Periodic Inspections: Periodically examine the external condition and functionality of the regulator to ensure the integrity of its parts and confirm there are no leaks.
- Cleaning Components: Dust and environmental pollution can disrupt the regulator’s function. Use appropriate tools and non-corrosive cleaning agents to clean the components effectively.
- Pressure Testing: Regularly measure both the input and output pressure using accurate instruments to ensure the correct calibration of the regulator.
- Replacement of Worn Components: Components such as diaphragms, springs, and internal components exposed to wear should be replaced on time, following the manufacturer’s guidelines.
- Using Gas Filter: Installing a filter in the gas inlet helps prevent the entry of particulate matter and protects the regulator from potential damage.
- Compliance with Manufacturer Guidelines: Always adhere to the manufacturer’s instructions and avoid unauthorized repairs.
- Specialist Review: If issues such as decreased accuracy, gas leakage, or pressure drop are noticed, consult specialized technicians for repair.
Following these recommendations contributes to improved safety, lower maintenance expenses, and a longer service life of the regulator.
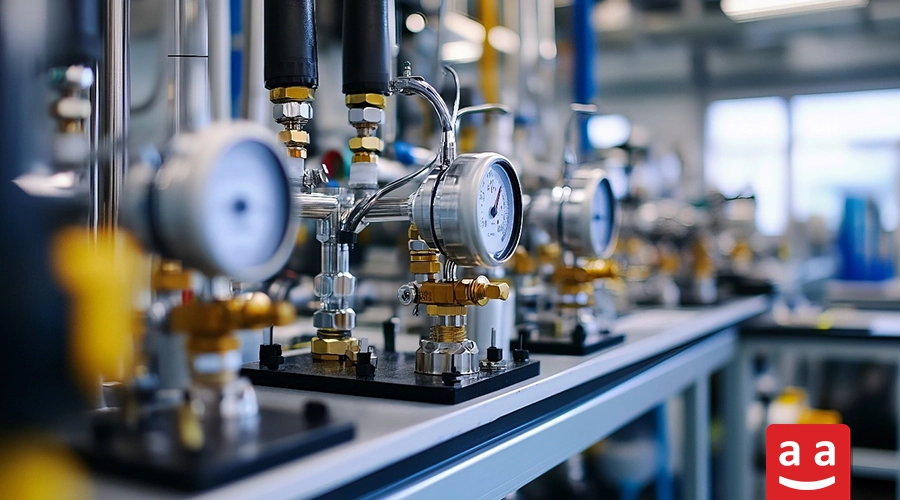
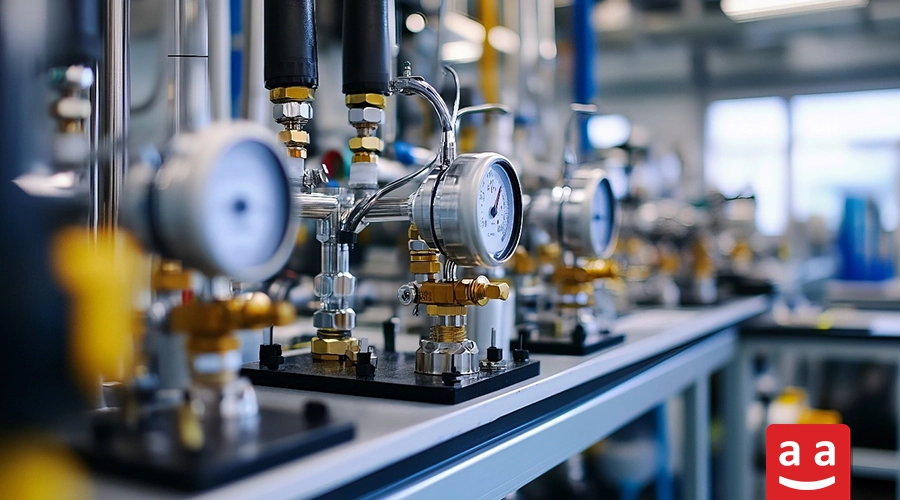
Gas Regulator; An Intelligent Choice for Seamless Operation
Gas train regulator is a crucial component in natural and industrial gas distribution systems, responsible for regulating and controlling gas pressure. There are various types of these devices available in the market, including low-pressure, medium-pressure, and high-pressure regulators, each designed for specific applications. Choosing the right regulator for a system depends not only on the application type and system requirements but also on selecting a reputable brand. Opting for reliable brands with after-sales services and international standards is recommended to ensure optimal and flawless long-term operation.